
Will our computers learn to think?
Europe has finally recognised the importance of the circular economy as a means to tackle climate change
Read more

Playing it safe
Europe has finally recognised the importance of the circular economy as a means to tackle climate change
Read more

Environmental education: a subject for big and small!
Europe has finally recognised the importance of the circular economy as a means to tackle climate change
Read more
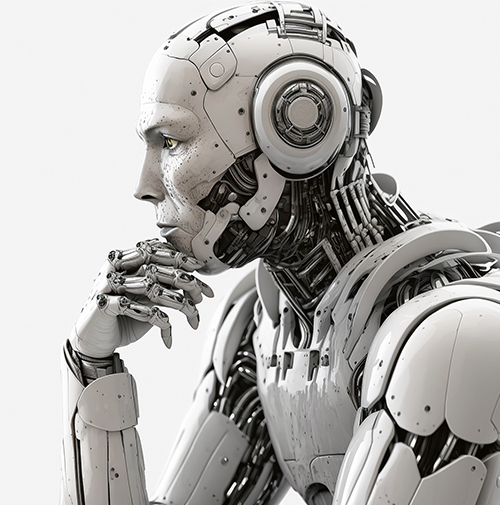
18. April 2024
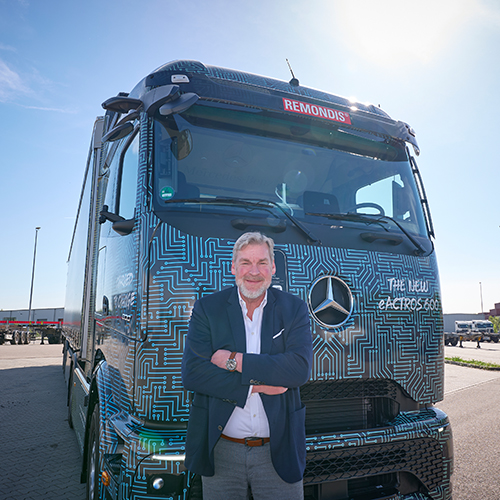
17. April 2024
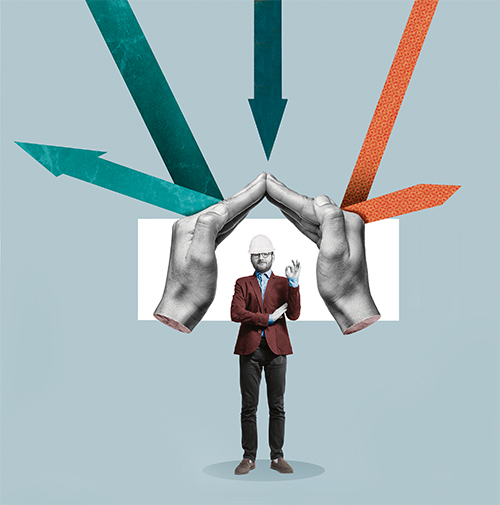
26. March 2024
Newsletter
Use this simple way to sign up to our REMONDIS AKTUELL newsletter containing information about your services, products and other information.
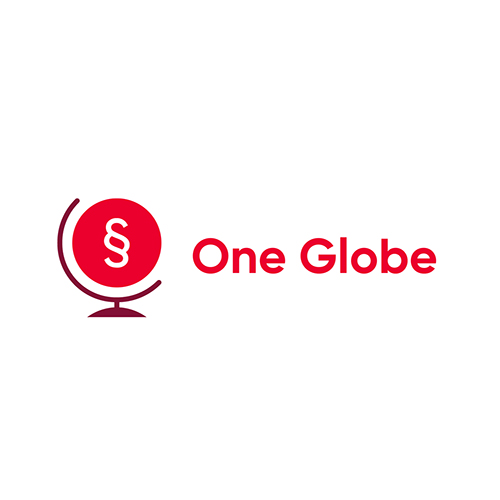
25. March 2024
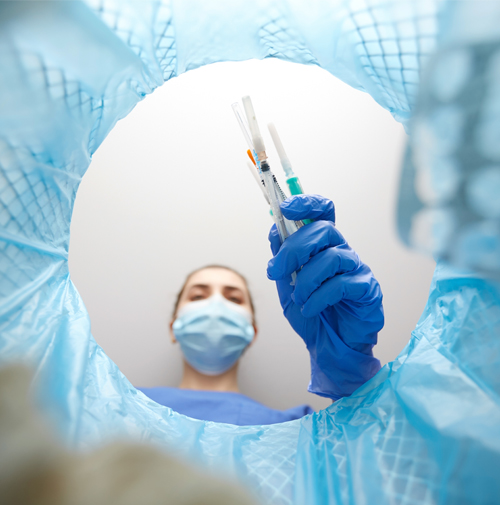
21. March 2024
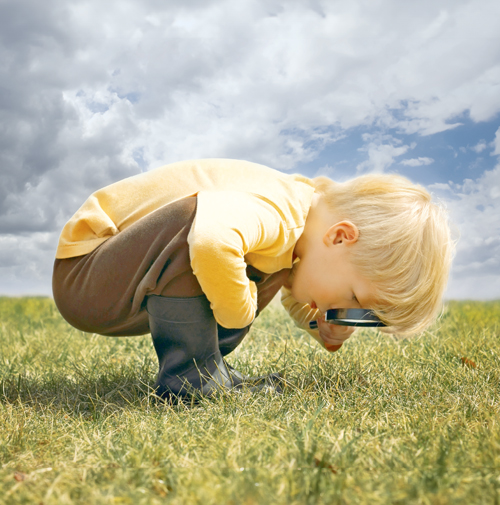
6. March 2024
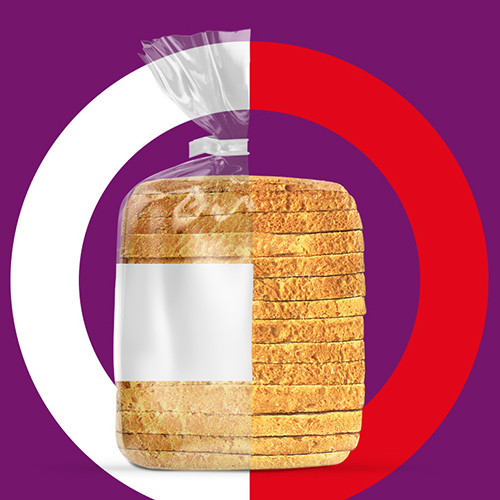
6. March 2024